Not only the adhesive tape bonds. The going also gets tough within the adhesive tape: the primer ensures that the adhesive sticks to the backing material really well. And if you think that the ease with which adhesive tape unrolls depends only on your muscles – you're wrong. The separating layer – also called release coating – of adhesive tape greatly helps in the process.
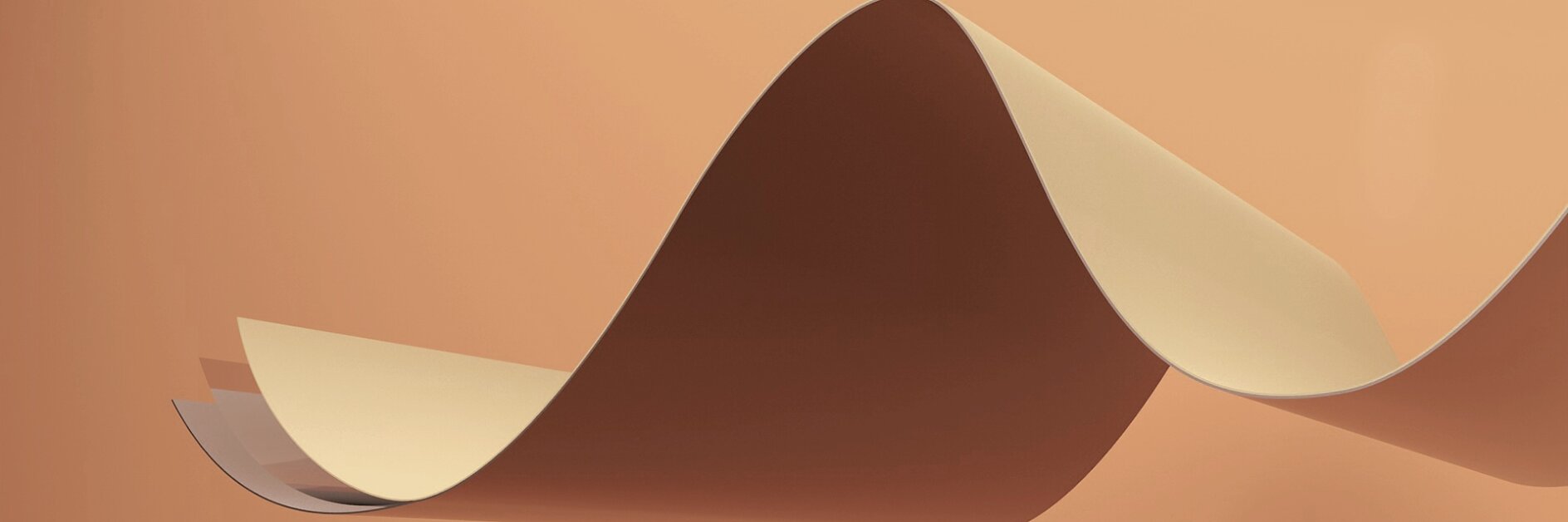
What is so exciting about adhesion bonding primers, release coatings and liners?
Technologies
Primers (adhesion bonding primers) play an important role in adhesive tape. In addition, release liners and release coatings (separating layer) ensure perfect unrolling.
What is a primer (adhesive primer)?
Adhesive tape consists of two important components: the adhesive, which bonds in the form of a pressure-sensitive adhesive on the adhesive tape and is sticky throughout. And the backing (paper, film, fabric, fleece, etc.), which holds the adhesive. Now there are adhesive tapes for many different purposes. They differ in terms of speed, length and solidity of the bond.
And this is exactly where primer comes into play. It is a thin layer that is applied to the bottom of the backing and reinforces the adhesion of the adhesive. The adhesive tape bonding primer is always used if the adhesive should adhere especially strongly to the backing. This makes sense if the adhesive tape is only attached temporarily and no glue residues should remain after removing it – with masking tape, for example.
Or if adhesive tape should bond two things for ever. The increase in adhesion allows mirrors attached with adhesive tape to stick to the wall. Without the primer or adhesion bonding primer or even an anchoring aid, the adhesive might not glue strongly enough to the backing of the adhesive tape and let the mirror fall from the wall.
Structure of single-sided and double-sided tape
Structure of single-sided (left) and double-sided (right) adhesive tape: 1) Release coat, 2) Backing, 3) Primer, 4) Adhesive, 5) Release liner (Silicon coated), 6) Adhesive (closed side), 7) Primer, 8) Backing, 9) Primer, 10) Adhesive (open side)
Better adhesion with primer
The actual service of the primer becomes clear when we put the backing under the microscope. The backing should hold the actual adhesive on the adhesive tape. Often, the backing consists of plastic, for example, because that is the most sensible solution for this area of use. However there are plastics and other materials which adhesive does not stick well to. Polyethylene (PE), polypropylene (PP), Teflon, rubber and silicone are some of these. Experts speak of "very low surface energy." The actually "exciting" thing about a primer is: it increases this surface tension, which lets the backing and the adhesive stick to each other more strongly.

The second specialist in the group: the release coating/liner (separating layer)
There is a second component that makes adhesive tape a situational specialist. Some adhesive tapes have special separating layers, the 'release coating' and the 'release liner', on the top side, so that the adhesive tape on the roll does not stick to the layer above it. A release liner is mainly used with double-sided tapes. Siliconized papers or films are the main types of release liners. The optimal liner choice depends on the application. If die-cut ability is required, polyester liners are preferable. If the tape is exposed to humidity, poly-coated papers are mainly used due to their dimensional stability. For most applications, paper liners are the liners of choice.
The backing of a single-sided tape, and the release liner for a double-sided tape, are treated with a release coating. The release coating ensures stable unwinding of the tape during the application. This is very important for automatic applications in which the tape can be unwound at high speeds. A release coating can have different release forces for either easy unwinding or harder unwinding, depending on the customer’s needs.
Release liners for double-sided tapes
The adhesive-repellent liner is needed to be able to unwind and properly apply the tape. The material can be either a plastic film or a special paper:
- Glassine paper: Standard solution
- PE-coated paper: Humidity-resistant
- MOPP film: Mainly for die-cuts and automated processes
- PE film: Mainly for foam tapes
- PET film: Mainly for high-precision die-cuts in the electronic industry
Material | Characteristics | |
---|---|---|
Glassine paper | ▪ Hand-tearable ▪ Good tensile strength ▪ Good electrostatic discharge |
▪ Stable under pressure due to hard paper core ▪ Die-cuttable ▪ Cost-efficient |
PE-coated paper | ▪ Better dimensional stability ▪ PE layer prevents moisture absorption ▪ Hand-tearable |
▪ Good tensile strength ▪ Good electrostatic discharge ▪ Die-cuttable |
MOPP film | ▪ Dimensionally stable, good tensile strength ▪ Humidity resistant |
▪ Small thickness tolerance ▪ Die-cuttable ▪ Translucent |
PE film | ▪ Very flexible for winding thick products | ▪ Humidity-resistant |
PET film | ▪ Temperature-resistant (max. 150°C) ▪ Good thickness tolerance |
▪ Dimensionally stable, thin ▪ Die- and kiss-cuttable ▪ Transparent |