The liquid packaging board industry is greatly affected by changes within our socio-economic environment. As such, the European Union’s August 2017 report expressed that one third of all households within the European Union in 2016 were single-person households, a statistic which corresponds with the market trend regarding smaller packaging. This, combined with an exploding demand for new flavors in the convenience food and beverages sector, has helped propel the liquid packaging board industry into a state of creative flux.
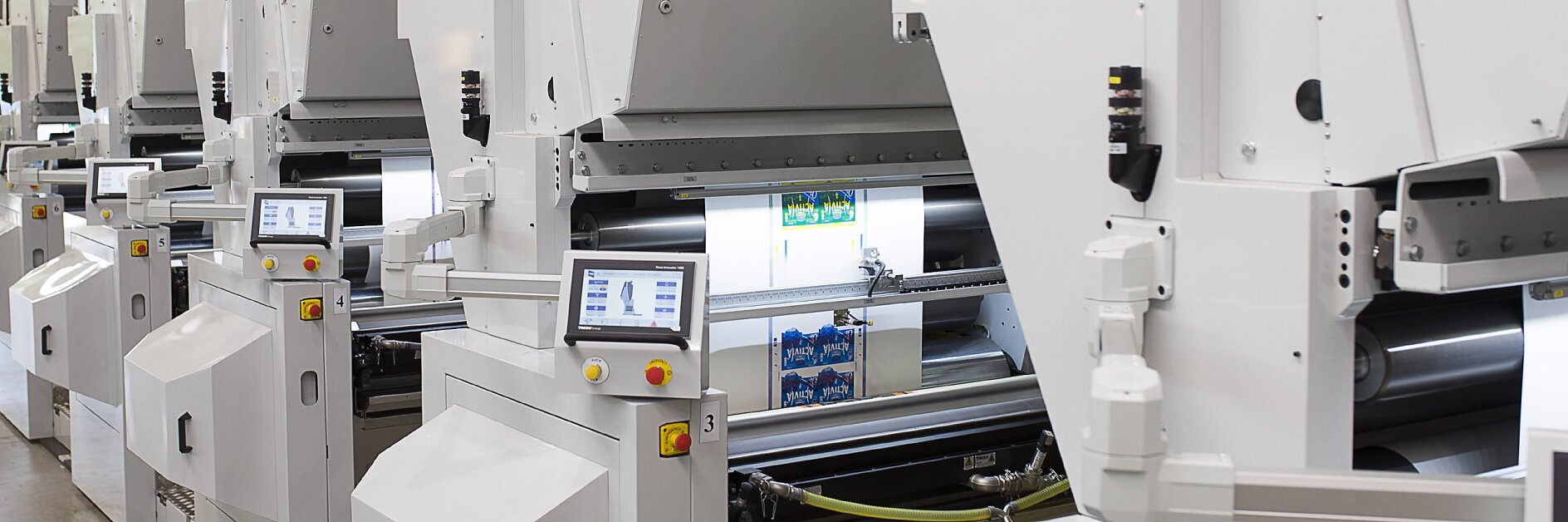
tesa Softprint® Performance Check on TRESU Flexo Innovator Press
Technologies
To prove our influence on print quality we tested our tesa Softprint® plate mounting tapes at TRESU's technical center.
What is the impact for liquid packaging board printers?
In order to increase the visual effects of smaller packaging sizes to attract more consumers, packaging designers are working on more challenging and creative design elements, all of which lead to higher print quality requirements. The increasing number of unique and complicated product designs push the industry to re-think existing production methods. This is vital in giving producers the opportunity to react to changing conditions and remain efficient and competitive in the market.

Proof of performance on the TRESU INNOVATOR PRESS
To prove our influence on print quality we often test our tesa Softprint® plate mounting tapes on-site, at industry leading print manufacturers. One of the latest tests was performed in the technical center of TRESU Group in Denmark. The goal was to evaluate the print quality on paper carton board when using different foam hardness levels.
The trial was conducted on the TRESU FLEXO INNOVATOR PRESS with a 6 color (CMYK + 2 spot colors) test form. This printing press is designed to print on a variety of paper board material and thanks to TRESU's innovative machine concept, fast job changes with low waste rates can be achieved.
The outcome of the print test
The general belief regarding foam hardness is that plate mounting tapes with harder foams are recommended for solid motifs while plate mounting tapes with softer foams are recommended for screen motifs.
foam hardness
During the trial we tested our four main tesa Softprint® plate mounting tape hardness levels under identical conditions. For the printing plate, we used a 1,14 mm Kodak NX plate with 60L/cm and an anilox roller with 400L/cm and 4,6 cm³/m².
The evaluation of the samples showed that the SOFT Foam (red color code) produced the best results. Even on solid prints, low dot gain and equal ink laydown without pin-holing effects were achieved.
Low dot gain and perfect dot shape with soft foam hardness
Ink lay down on solid print using soft foam hardness
Foam Hardness Level | Measuring Field [%] | Dot Gain Value [%] | Density | Measured in Color |
Hard | 50% | 17.8% | 1.57% | Cyan |
Medium-Hard | 50% | 17.5% | 1.55% | Cyan |
Medium | 50% | 15.6% | 1.53% | Cyan |
Soft | 50% | 14.6% | 1.50% | Cyan |
Conclusion
The outcome of the print samples produced results that slightly differed from the expected theoretical outcome. The reasons for this mainly relate to the paper, which behaves differently from materials such as film during flexible packaging printing. In addition, the printing plate technology used (Kodak NX) has micro structures (or enhanced surface technologies) which provide a particularly high ink transfer to the substrate. These factors have to be considered when selecting the appropriate anilox roller and plate mounting tape foam hardness.
When these individual components are perfectly coordinated, the whole process is significantly simplified, leading to a more streamlined and efficient process, and ultimately higher print quality.
If you want to know more about our tesa Softprint® products or TRESU Group flexo printing presses please contact your responsible tesa® and TRESU sales representative.